It can now, thanks to the innovation of Finkl Steel, which is focused on solving more problems than just fluid end life.
Can a forging REDUCE your carbon footprint?
Reduced Cost. Reduced Lead Time. HVX Reduces Over 89 TONS of CO2 Per Heat!
Reduced Cost. Reduced Lead Time. HVX Reduces Over 89 TONS of CO2 Per Heat!
Reduced Cost. Reduced Lead Time. HVX Reduces Over 89 TONS of CO2 Per Heat!
Reduced Cost. Reduced Lead Time. HVX Reduces Over 89 TONS of CO2 Per Heat!
Reduced Cost. Reduced Lead Time. HVX Reduces Over 89 TONS of CO2 Per Heat!
Reduced Cost. Reduced Lead Time. HVX Reduces Over 89 TONS of CO2 Per Heat!
Reduced Cost. Reduced Lead Time. HVX Reduces Over 89 TONS of CO2 Per Heat!
Reduced Cost. Reduced Lead Time. HVX Reduces Over 89 TONS of CO2 Per Heat!
At Finkl Steel, we have been innovating steel products for over 100 years to overcome the challenges of the time. Today’s challenge is to REDUCE NICKEL VOLATILITY and REDUCE OUR CARBON FOOTPRINT for ourselves and our client’s products. HVX Stainless was designed for fluid end consumers to do just that.
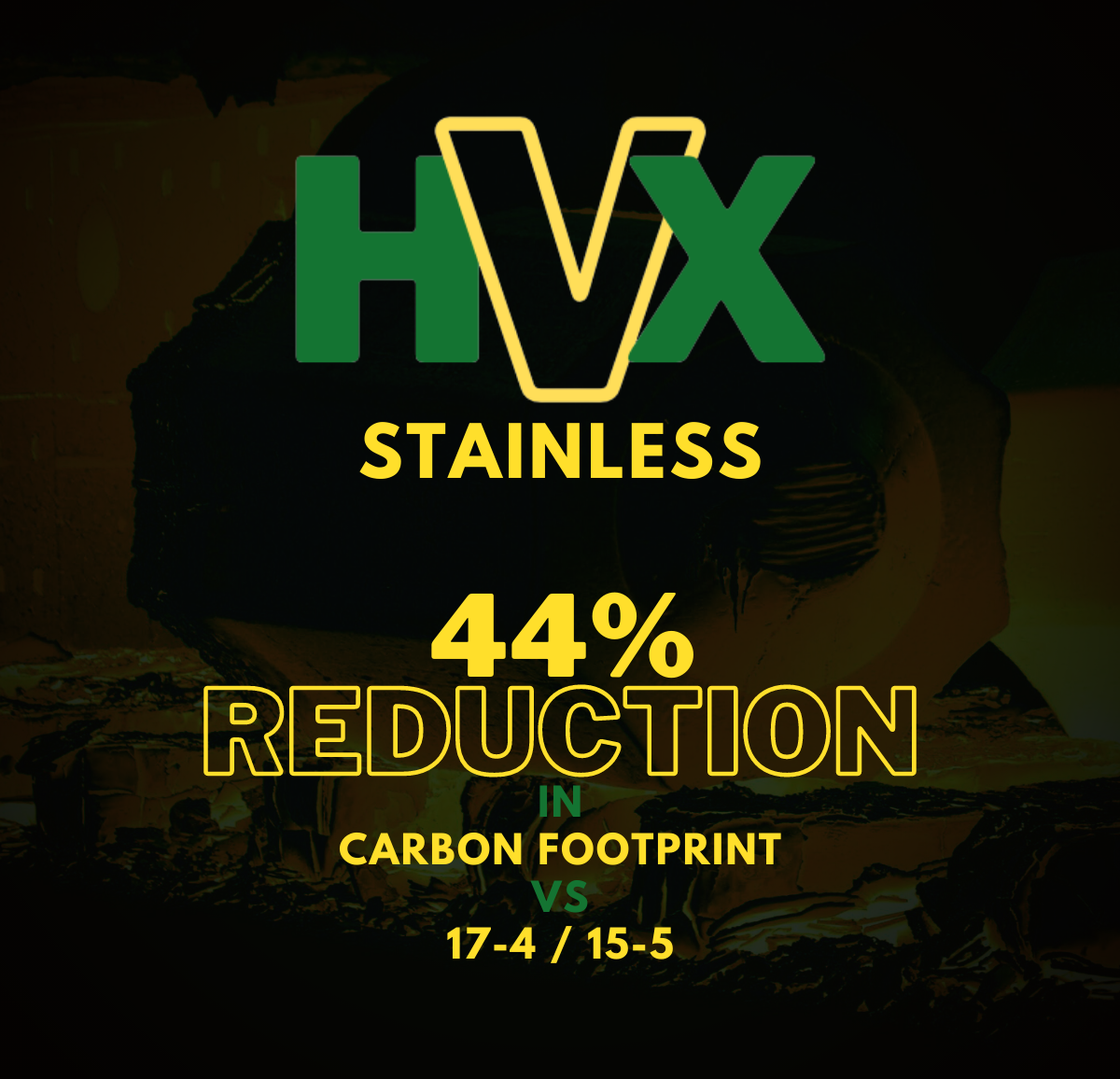
HVX STAINLESS
How do you set out to make a stainless steel for fluid end forgings that reduces a carbon footprint? You have to start with performance. As a leader in fluid end forging manufacturing, Finkl Steel has an intimate understanding of the end-use application and properties needed during hydraulic fracturing. It is this domain expertise that was drawn on to create a specific grade of stainless steel that provided proper corrosion resistance while optimizing strength, toughness, and other mechanical properties. Through multiple field trials, the performance speaks for itself, achieving over 1,500 hours of operation in today’s highest pressure.
MADE IN THE USA
EVOLUTION OF HVX
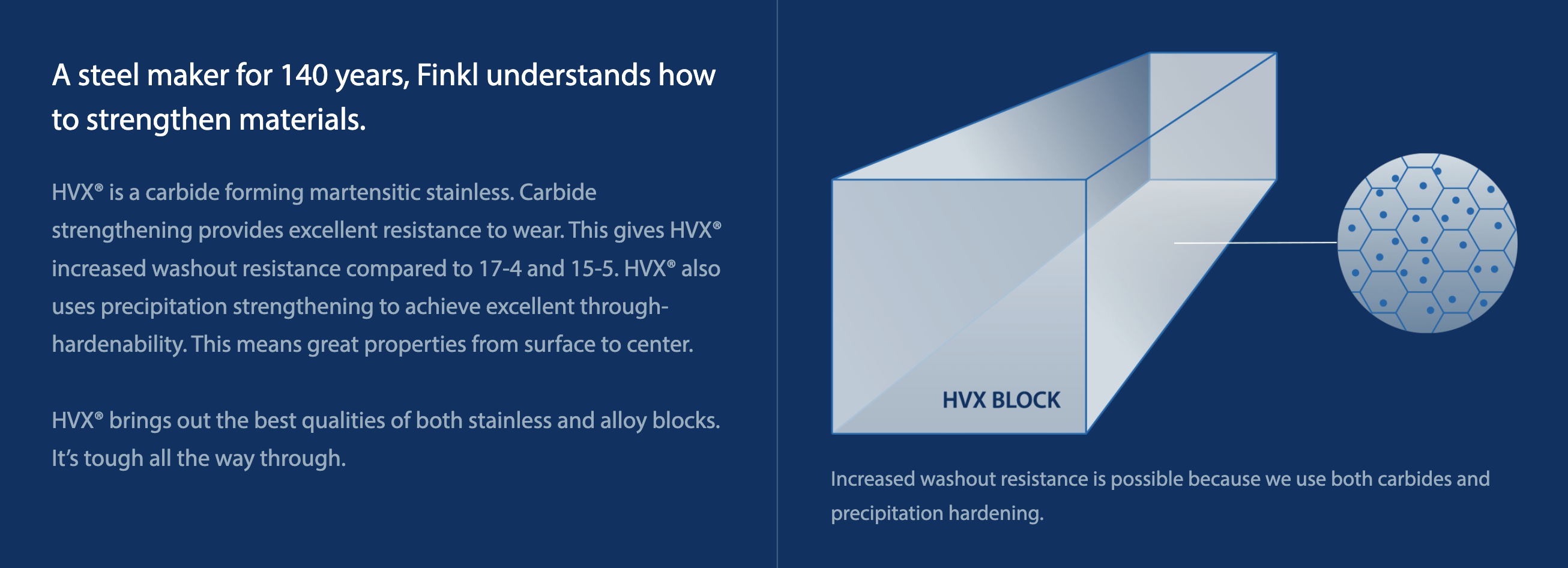
In order to develop HVX® Stainless, our metallurgists researched the different stainless alloy families and tested many variations in chemistry. They found the ideal mix and concentration of elements that bring out the best properties of both martensitic and precipitation strengthened stainless steels. The result is a stainless formula that contains a fraction of the quantities of some of the most expensive elements while still matching, and often exceeding, the more expensive grades in fracking performance.
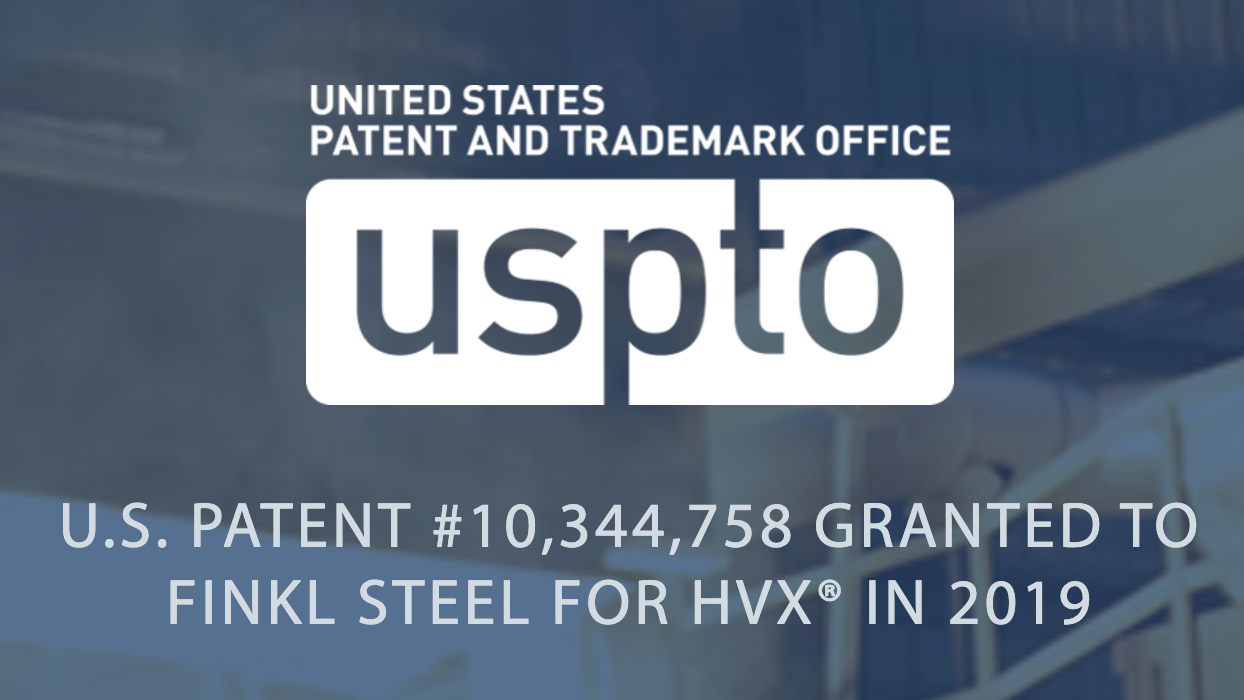
LESS NICKEL
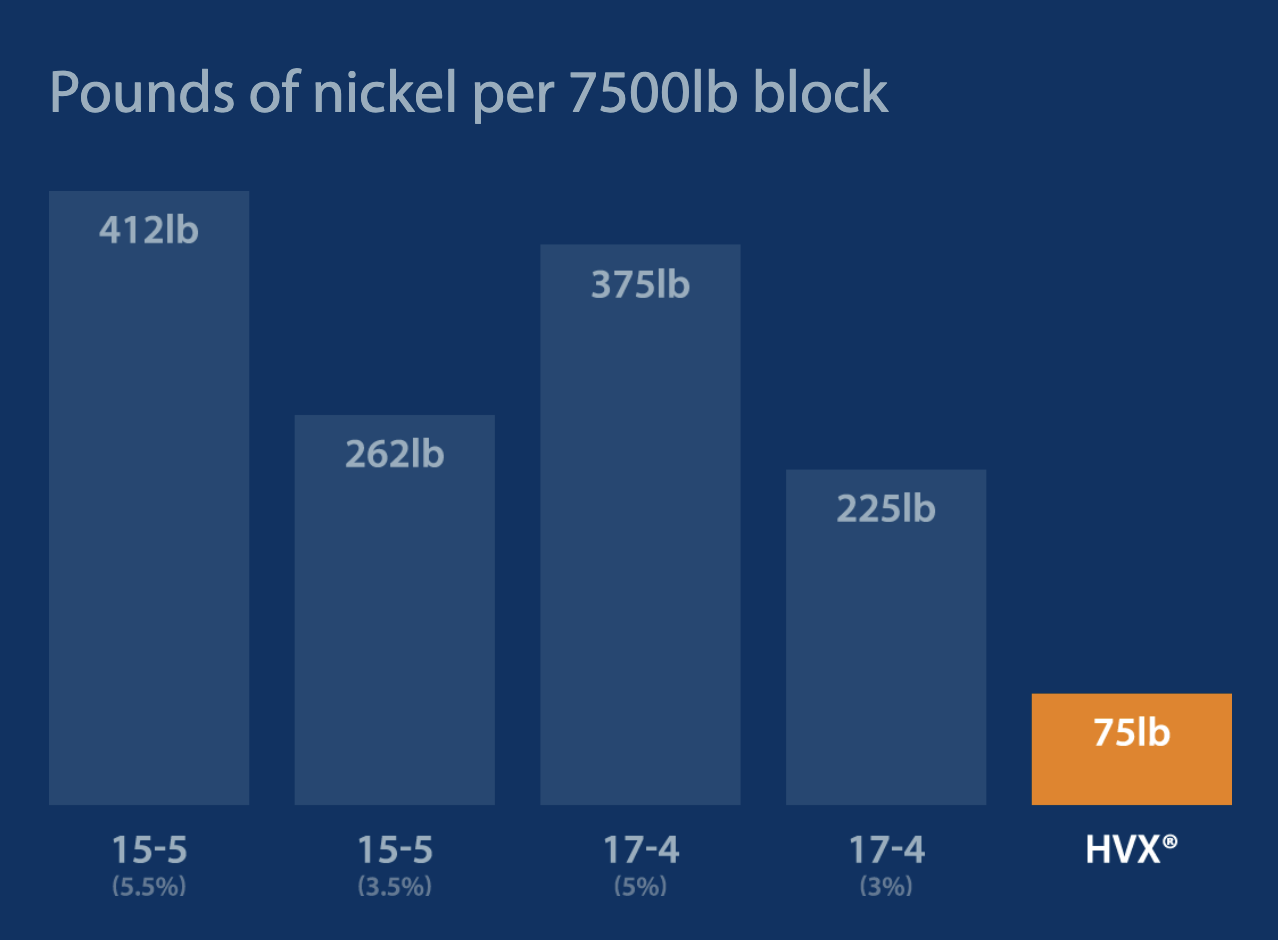
For example, nickel makes up around 5% of a 7,500 pound block of 17-4 or 15-5 stainless. What we found is that nickel at 1% concentration together with an optimized amount of other elements and processed correctly gives HVX® Stainless the right combination of properties for superior performance.
The difference means that companies won’t need to pay for 300 pounds of nickel that don’t create additional service life. As prices of nickel are taking off and projected to skyrocket, HVX® Stainless becomes the ultimate hedge against PH stainless price increases.
CORROSION RESISTANCE
HVX® Stainless is designed with the preferred chemistry to resist corrosion in harsh environments. It doesn’t compromise.
When people first look at HVX® Stainless on paper and compare the Charpy values to 17-4 and 15-5 they may think it is not tough enough. What they miss is that in real-world conditions a lab-tested impact strength value is just one of many key variables. If abrasion and erosion break down the protective stainless surface and corrosion sets in, then cracking will occur regardless of the impact strength.
Pitting Resistance Equivalent Number (PREN) is the measure for predicting a steel’s resistance to pitting corrosion. PREN is calculated based on the chromium, molybdenum and nitrogen content of the steel. These elements contribute to form a passivating layer on the surface of the steel that protects it from corrosion.
Alloying with molybdenum to increase the PREN with 17-4 and 15-5 is less than ideal because it promotes the formation of a brittle and crack prone microstructural phase called delta ferrite. With HVX®, we’ve optimized the chemistry and process so we can alloy with moly without this risk and boost the PREN.
But it’s important to understand that PREN alone can’t do anything against abrasion. High PREN combined with low abrasion resistance can result in the same life as low PREN and high abrasion resistance. With HVX® you get the benefits of the passivating moly oxide film and the wear resistance of moly carbides. You get all the PREN you need and better protection against the abrasive wear that reduces corrosion resistance.
So why pay extra for the increased nickel content of PH stainless grades when there is no additional benefit? HVX® Stainless is more than tough enough.
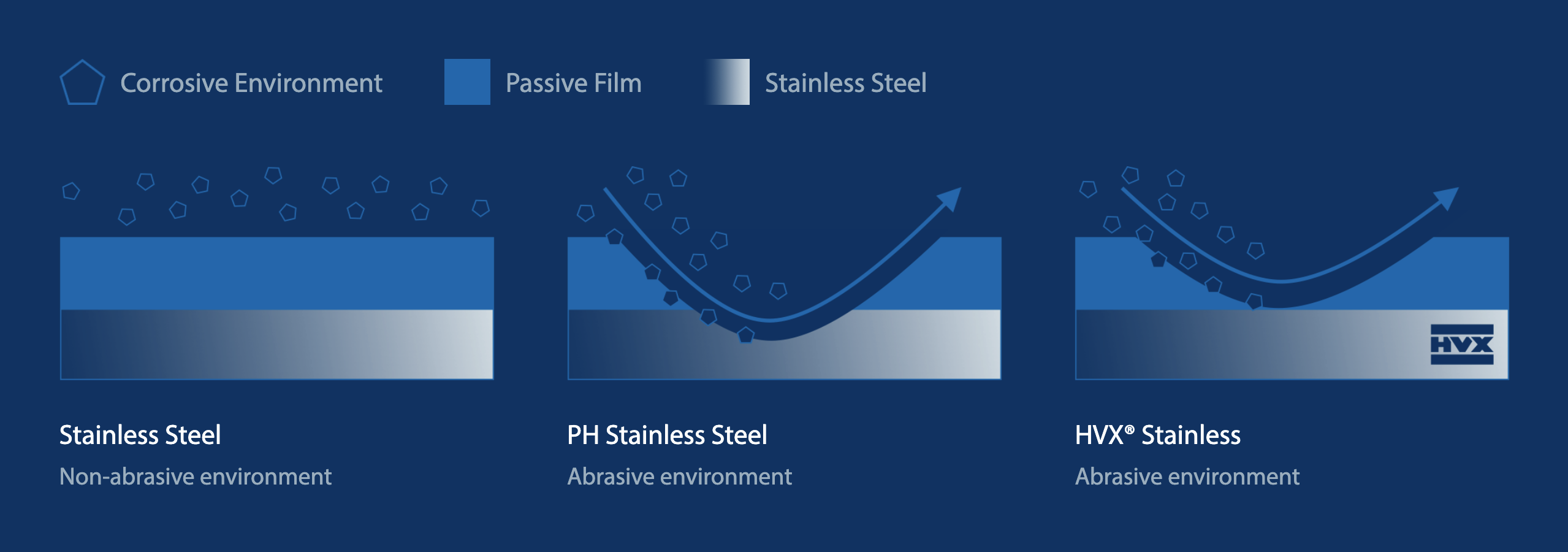
FASTER MACHINING
Besides the actual cost for a block, fluid end manufacturers spend a great deal of time and money on machining. HVX® Stainless is already proven to be hard enough for the field, but it is also designed for faster machinability.
HVX® Stainless is saving some fluid end manufacturers over 25% on the amount of time it takes to make a fluid pump in comparison to 17-4 and 15-5. This makes it easy for them to try HVX® Stainless and then add it to their catalog of offerings. Another key benefit is that it reduces their lead time to make a pump end so they can serve well service companies even better.
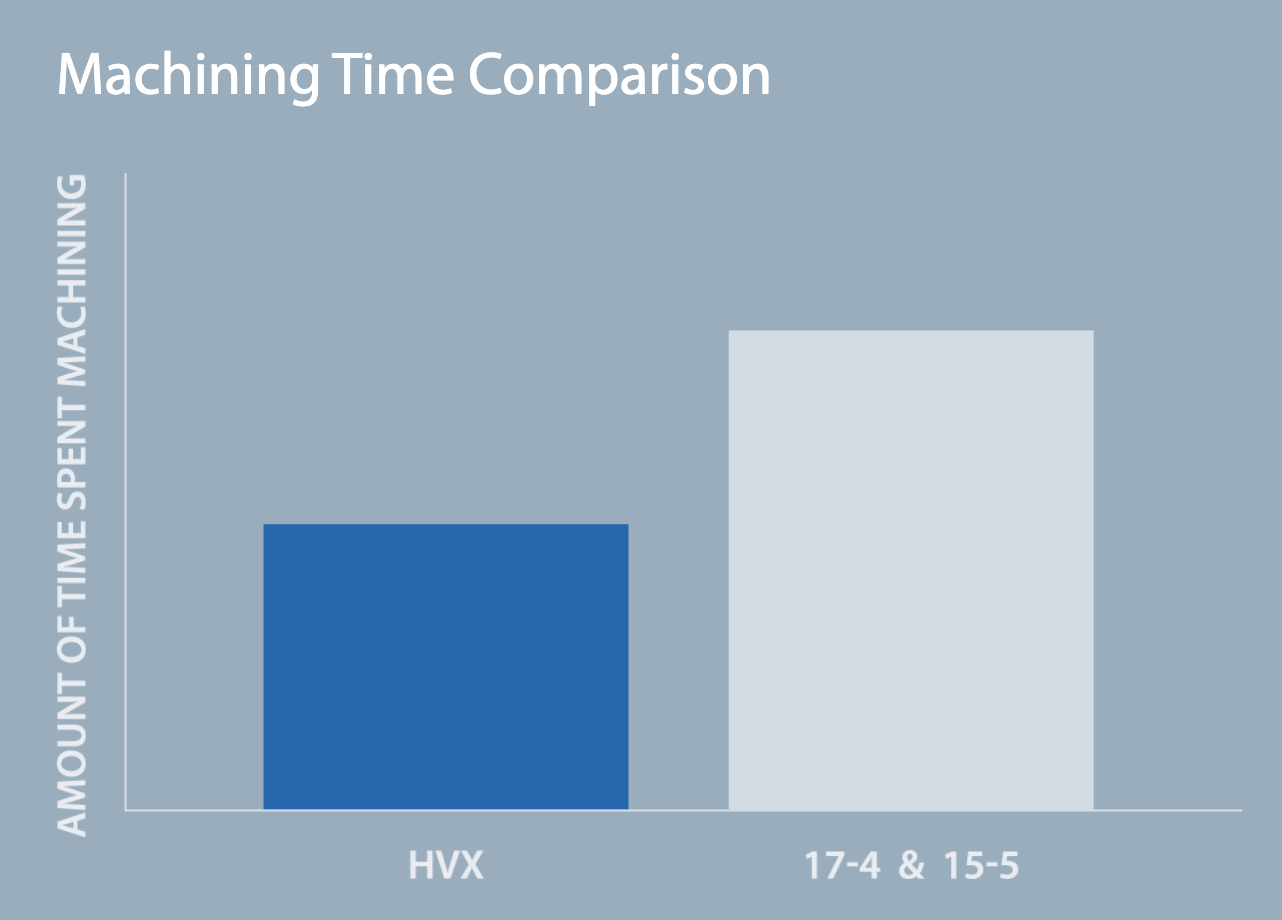
FASTER LEAD TIME
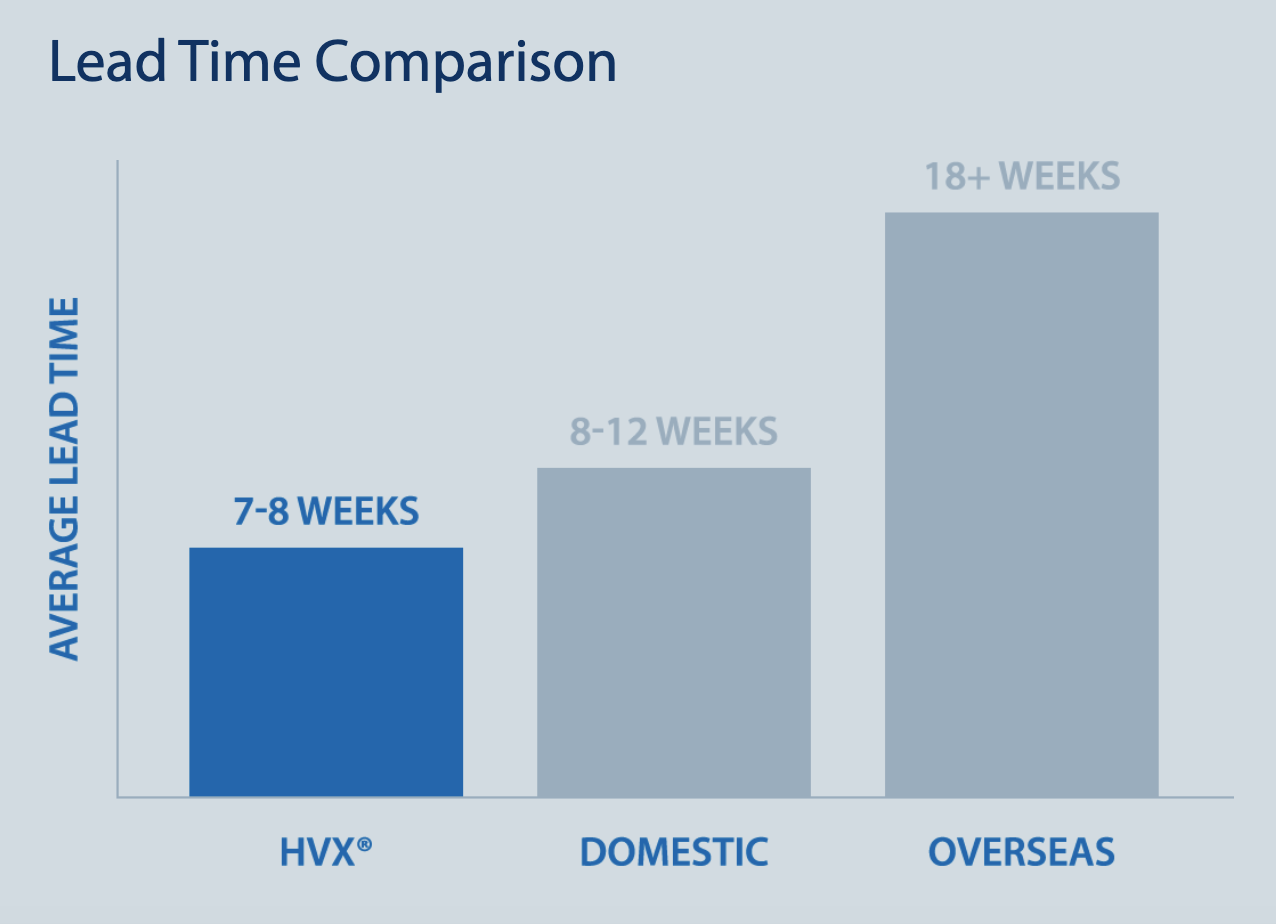
HVX® Stainless eliminates the need for holding safety stock and having to forecast far into the future the number of fluid ends you will really need. This is possible because Finkl has a dedicated “lean line” in Chicago just for HVX® Stainless.
We created this so the lead time for a new HVX® Stainless block will always be just 7-8 weeks. This is much faster compared to most forging suppliers. On top of this, the HVX® lean line capacity can be flexed to produce up to 6,000 HVX® blocks per year.
ACTUAL CARBON REDUCTIONS
After proving the quality and field performance of the material, Finkl Steel started focusing on reducing the carbon generating activities when manufacturing stainless steel fluid ends. They specifically set out to reduce the melt time, the number of furnace re-heats, total die time, and machine times. The final modifications to this material have created a stainless steel, optimized for fluid ends, that reduces the carbon footprint of each heat by over 44%.